SLR SERIES
Heavy-load robots
Heavy-load robots speed up handling and make it safer and much more reliable than non-robotized operation.
Where standard industrial robots reach their limits in terms of load carrying capacity and reach, our heavy-duty robots feel at home.
HIGHLIGHTS
Heavy-load robots of the SLR series are the tools of choice for frequently recurring handling operations, such as the transfer of forgings between the furnace and the press as well as the loading and unloading of rotary hearth furnaces.
They are specially designed for use in forging and ring rolling shops, in other words, for heavy loads, high-temperature environments and applications that require a long reach.
Stationary SLRs are particularly suitable for recurring transfer operations between close locations, such as a press and a nearby furnace. In such an application, a stationary robot is unparalleled in terms of handling precision and speed.
Rail-bound robots on the other hand are able to cover longer distances. A typical application would be the transport of forgings between several process stages.
The benefits at a glance
- Long reach, even with heavy forgings
- Compact design
- Precise, high-speed actuation
- Perfectly linear lifting and feed movement
- Fully automatic, semi-automatic and operator modes
Its versatile gripper tongs and its wide range of potential uses make the SLR an ideal machine for handling operations in closed-die forging shops. From the blank to the finished forged components most workpieces will be gripped with one and the same tongs. Nevertheless, handling flexibility can be further enhanced by using our quick-change tongs.
The adjustable gripping pressure is particularly useful in ring rolling, to ensure the finished rings will not deform while being transported.
When used in heat treatment operations, it's high actuation speed and fully automatic system guarantee short cycle times as well as excellent repeatability.
MORE DETAILS
Sophisticated kinematics
The positively controlled mechanics of the lever system and the accurate position control ensure perfectly linear motion of the tongs holder in both horizontal and vertical direction. This is achieved by the combined movement of two mechanically coupled levers. The lever system is torsion-resistant and designed for ease of maintenance.
Thanks to the multi-stage lever system, the SLR is perfectly suitable even for use in areas of very limited space.
Hydraulic or electro-mechanical
For the handling of loads exceeding 15 t our robots are hydraulically actuated. For lower-weight forgings we equip them with innovative electro-mechanical drives.
Using electro-mechanical drives means much less energy consumption thanks to the direct power input – without the detour via a hydraulic system.
Safe hold at all times
We supply the robots with tongs that best meet the specific application. For example:
- Tongs designed to grip discs, ring blanks and rings
- Tongs designed to grip ingots and forgings from above
- Tongs designed to set forgings upright
In addition to opening and closing as well as lifting and lowering, an optional rotary drive enables the robot to rotate the forging through its horizontal axis. Furthermore, the tongs can be tilted to pick up a forging from the floor, for example.
The adjustable clamping force assures that the forgings – rings, for example – do not deform during handling.
High flexibility
Thanks to the choice between three operating modes, the SLR provides maximum flexibility:
- Fully automatic operation: When used in large-volume series production runs where handling operations are repetitive and identical. The robots operate in automatic mode, controlled by a higher-level master computer.
- Semi-automatic operation: For parts of special shape and small numbers of parts, it is possible to switch over to semi-automatic mode. The machine may be positioned in front of the furnace in the automatic mode, for example. Then the operator takes over to pick up the workpiece. This accomplished, he may switch the system back to automatic operation.
- Operator mode: The operator controls all axes of the robot from the cabin via joysticks and other controls or from a separate control room via remote control and camera view.
User-friendly programming
The application programs are created and adapted via the touchscreen of the “Mission Editor” or via a mobile panel. Actuation and waiting commands are selected from pulldown menus. Positioning parameters may be entered as absolute or relative values or copied from the current position of the tongs via the teach-in function.
Safety first
The hydraulic accumulators assure that in the event of a power failure the tongs can still be safely retracted from the furnace. By integrating a hydraulic accumulator into the pressure line to the tongs cylinder, the clamping force of the tongs is maintained even if the system pressure decreases.
The operator cabin comes with effective noise and heat protection equipment as standard. The cabin can also be fitted with an industrial air conditioning system as an option.
Low energy consumption
The SLR robots fitted with an electromechanical drive feature low energy consumption. This is because they convert electrical energy directly into motion via the servomotor and/or the spindle.
During braking, the drives operate in generator mode. In other words, they generate power that can be fed to operate other loads via an intermediate circuit.
Technical data
Max. load capacity of the tongs up to
kN
Max. reach of the tongs up to
m
Number of actuating axes
Swiveling range
Unlimited
Contacts
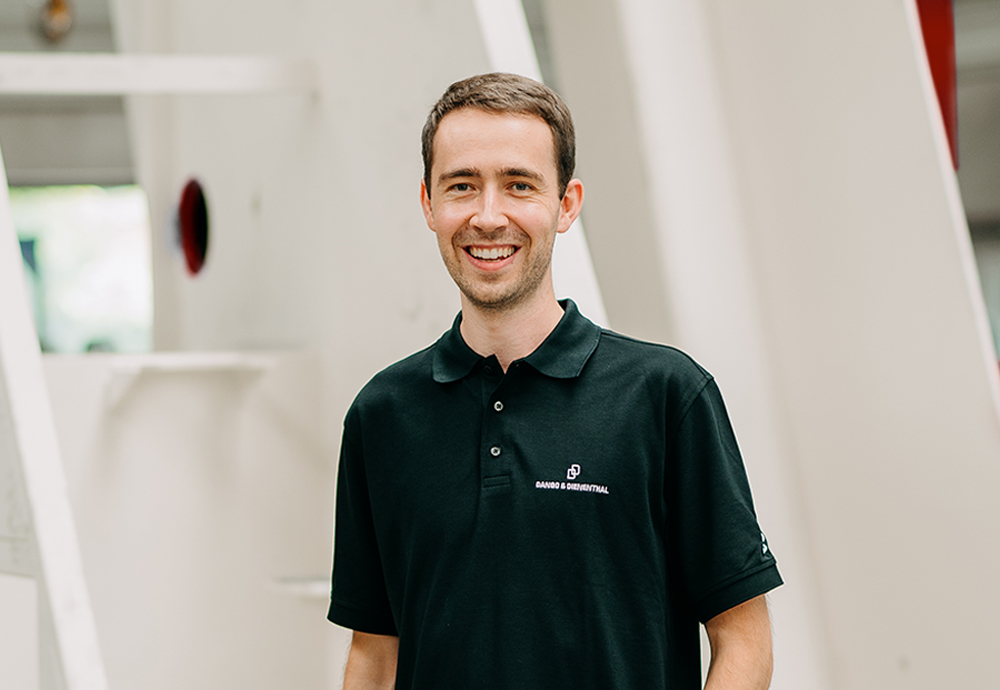
Herr
Andree Nöh
Senior Sales Manager
T +49 271 401-4491
andree.noeh@dango-dienenthal.de
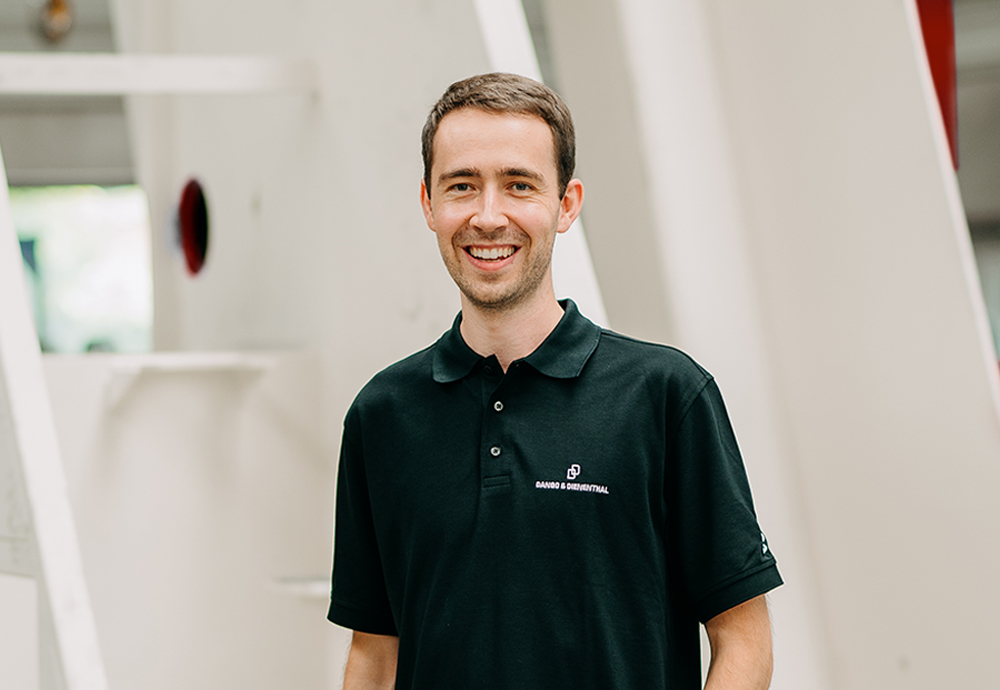
Herr
Andree Nöh
Senior Sales Manager
T +49 271 401-4491
andree.noeh@dango-dienenthal.de
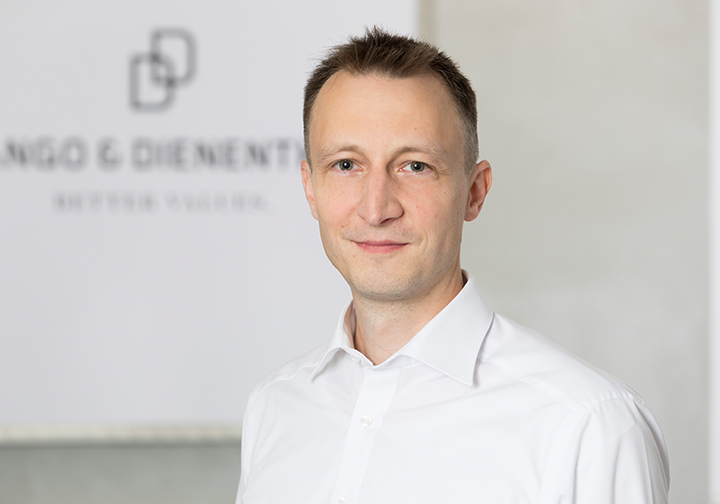
Herr
Boris Marcukaitis
Senior Sales Manager
T +49 271 401-4120
boris.marcukaitis@dango-dienenthal.de
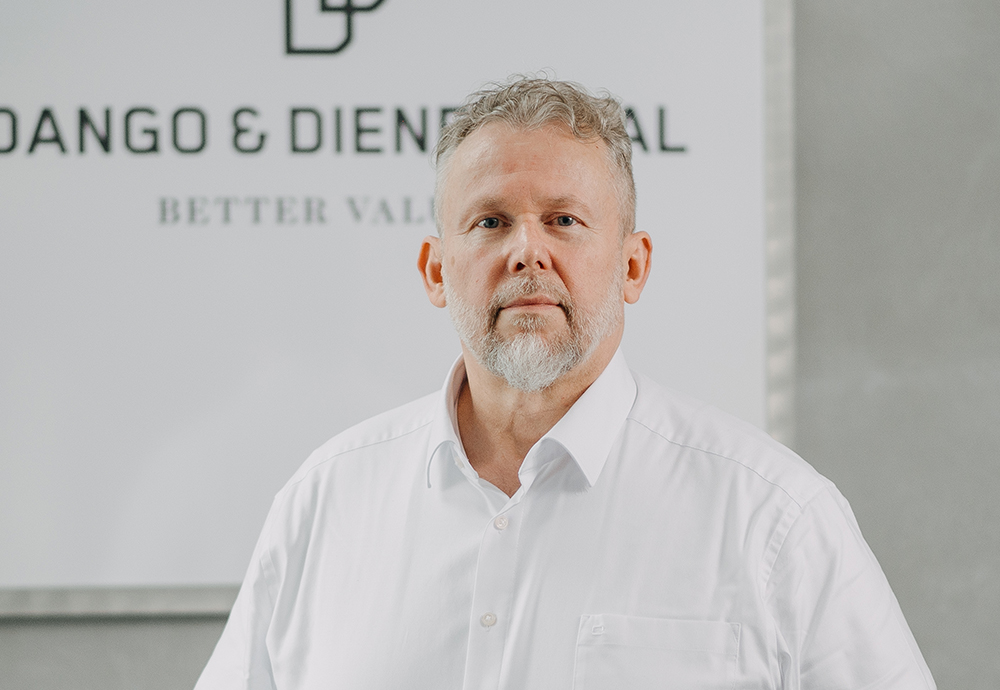
Herr
Volker Witzleb
Senior Sales Manager
T +49 271 401-4433
volker.witzleb@dango-dienenthal.de
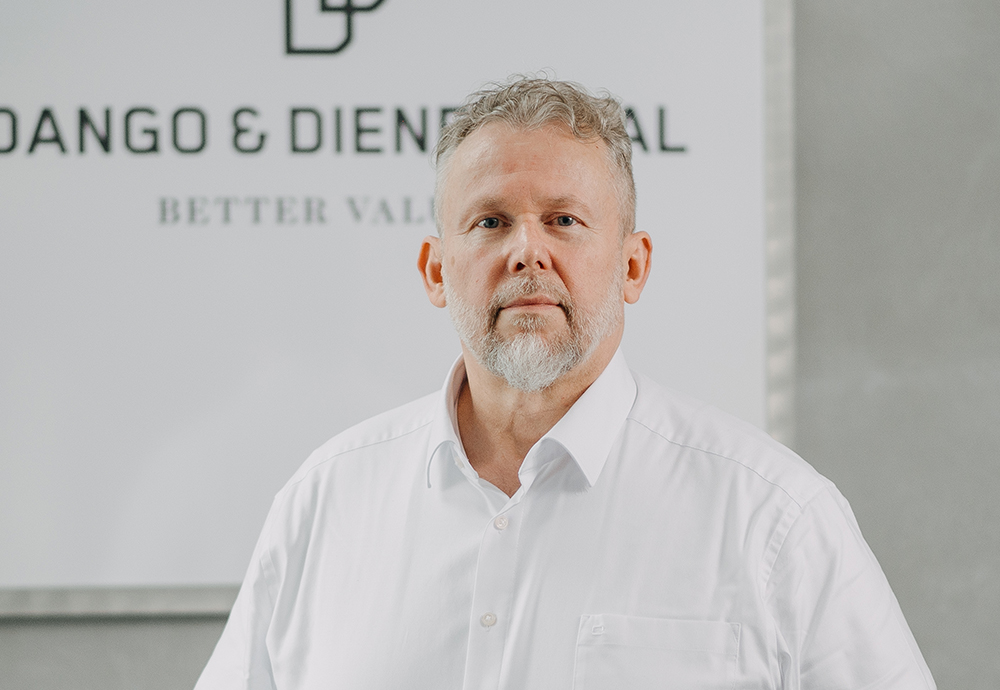
Herr
Volker Witzleb
Senior Sales Manager
T +49 271 401-4433
volker.witzleb@dango-dienenthal.de
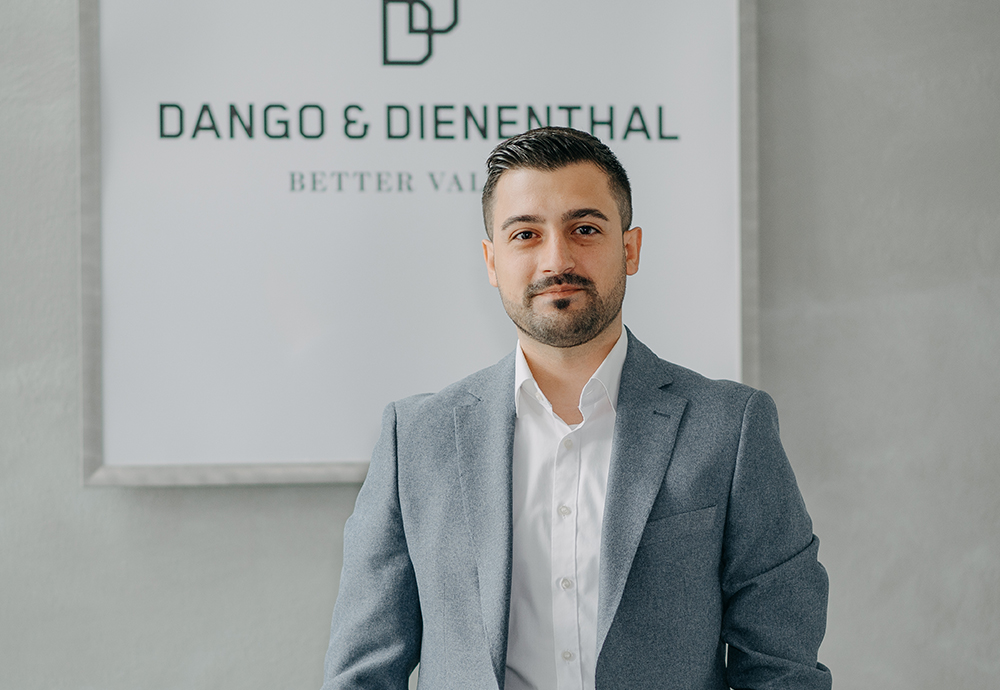
Iysa Demir
Sales Manager Service
T +49 271 401-4332
iysa.demir@dango-dienenthal.de